Welding Inspectors ensure that all the welding (New fabrications and Repairs comply with the applicable procedures.
Archives: Services
HDPE pipe line inspection
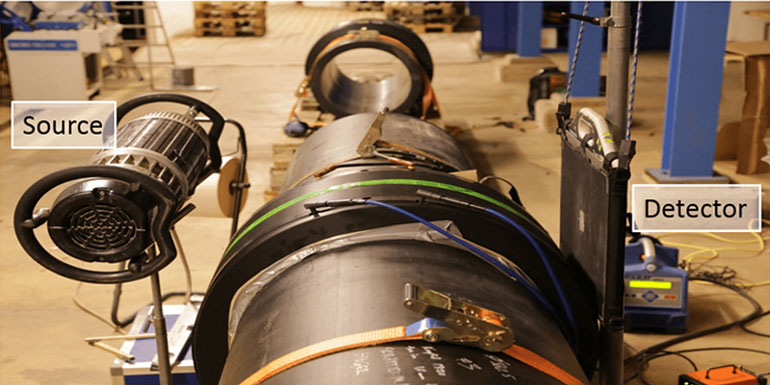
Digital Laser Profiling
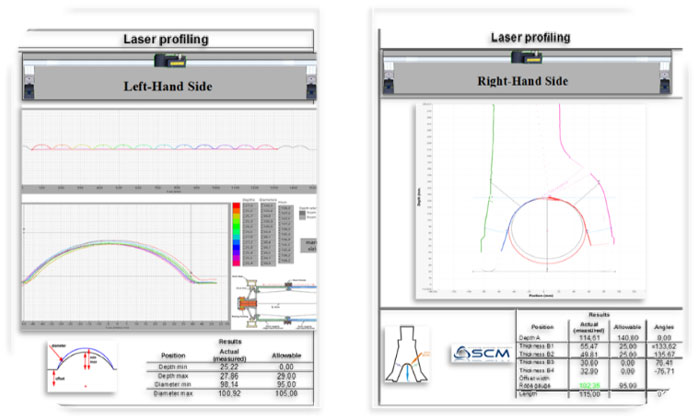
Accurate sizing and monitoring of Profiles. Using Advance Laser Sizing Technology. This technique is mostly used on Dragline Drums and Sheave Wheels.
What we do
Our Laser Profiling provide accurate measurements and dimensions. All our Laser Profilers are specifically designed for each job’s requirements and specifications.
Our service system
SCM Laser Profilers for Sheave Wheels and Grooved Drums
Hardness Testing
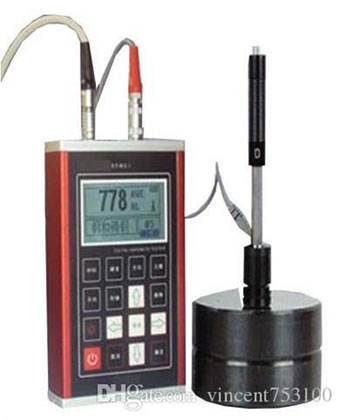
Hardness Testing Basics. Hardness is a characteristic of a material, not a fundamental physical property. It is defined as the resistance to indentation, and it is determined by measuring the permanent depth of the indentation.
What we do
Hardness Tests are extensively used to characterize a certain material, and to identify if it is appropriate for its intended purpose. All Hardness Tests involve the utilization of a particularly shaped indenter that is harder than the material under testing. The indenter is pressed onto the test surface with the use of a certain amount of force. The size of the depth of the indent is measured in order to determine the hardness value.
Benefits of Hardness tests:
- The Hardness Test is easy to conduct
- Results can be obtained within 30 seconds
- Tests are relatively cost-effective
- Finished components can be subjected to testing without being damaged
- Any shape and surface size can be subjected to testing
The major applications of Hardness Tests are to verify the type of heat treatment to be used on a part, and to identify if a material possesses the required properties for it’s intended use. This makes Hardness Tests beneficial in industrial applications.
The five most common hardness scales are:
- Knoop
- Vickers
- Rockwell
- Brinell
- Shore
Our service system
All our Hardness Testers are Calibrated and tested before each shift.
Our commitment
Is always to provide a precise and thorough inspection according to the Client’s requirement.
Most popular Questions
What is Brinell’s hardness test?
Brinell Hardness (BH) Test. Method of measuring the hardness of a material by pressing a chromium-steel, or tungsten-carbide ball (commonly one centimeter or 0.4 inch in diameter) against the smooth material surface, under standard test conditions (generally between 300 to 3 000 kilograms of force for 5 to 30 seconds).
What is hardness testing?
Hardness is a characteristic of a material, not a fundamental physical property. It is defined as the resistance to indentation, and it is determined by measuring the permanent depth of the indentation. The Rockwell Test is generally easier to perform, and more accurate than other types of Hardness Testing Methods.
How do hardness testers work?
A Hardness Test is typically performed by pressing a specifically dimensioned and loaded object (indenter) into the surface of the material you are testing. The hardness is determined by measuring the depth of indenter penetration, or by measuring the size of the impression left by an indenter.
Benefits of working with us
Based on experience we will always attempt to find an acceptable solution for any unconventional circumstances and needs.
Time of Flight Diffraction (ToFD)
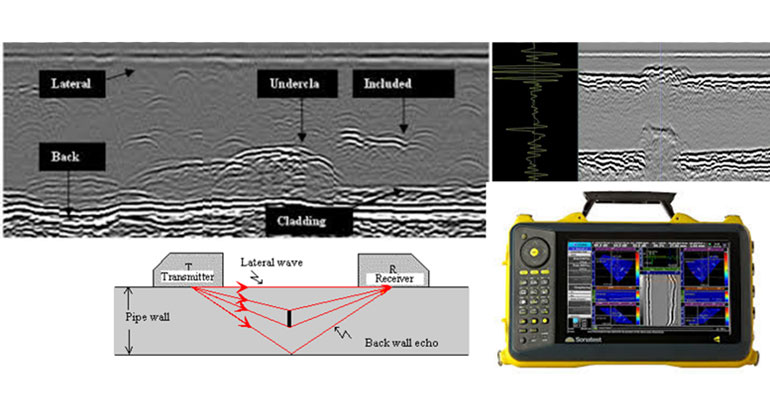
Measuring the amplitude of the reflected signal is a relatively unreliable method of sizing defects because the amplitude strongly depends on the orientation of the crack. Instead of amplitude, TOFD uses the time of flight of an ultrasonic pulse to determine the position and size of a reflector.
What we do
ToFD is an ultrasonic technique originally developed for crack detection. Unlike conventional Pulse Echo, the transmitter receiver in arrangement in ToFD floods the region between the probes with ultrasound. Crack tips are identified by diffraction but it is also very effective for the detection and sizing of Weld Root Erosion or Corrosion (WRE or WRC)
The nature of the reflection of the ultrasound from eroded/corroded areas in the TFD pitch-catch arrangement makes it ideal for the detection of Weld Root Erosion/Corrosion. This approach has a proven track record as an accurate method for the detection and monitoring of corrosion and erosion damage in the weld and heat affected zones.
Our service system
Sonatest VEO/VEO + & Prisma
Our commitment
Is to provide a precise and thorough inspection according to the client’s requirement at all times
Most popular Questions
What is Tofd inspection?
TOFD offers rapid weld inspection with excellent flaw detection and sizing capacities. The diffraction technique provides critical sizing capability with relative indifference to bevel angle or flaw orientation. TOFD can be utilized on its own or in conjunction with other NDT techniques.
What does TOFD stand for?
Time-of-flight diffraction (TOFD) method of ultrasonic testing is a sensitive and accurate method for the nondestructive testing of welds for defects. TOFD originated from tip diffraction techniques which were first published by Silk and Liddington in 1975 which paved the way for TOFD.
Benefits of working with us
Based on experience we will always attempt to find an acceptable solution for any unconventional circumstance
Manual and Automated Phased Array Inspection
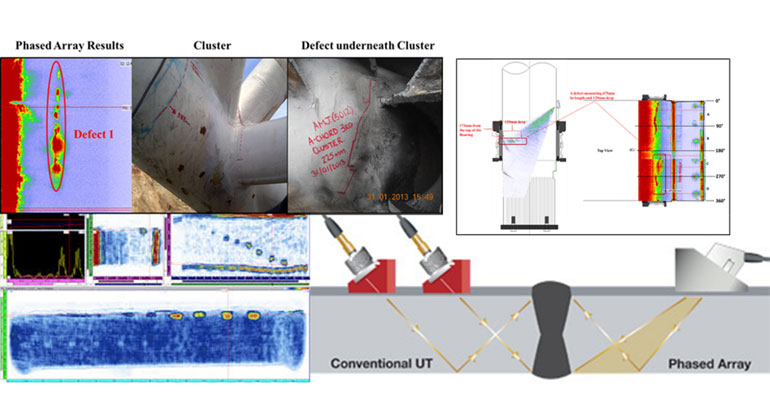
(PA) is an advanced method of Ultrasonic Testing that has applications in Medical Imaging and Industrial Non-Destructive Testing. Common applications are to non-invasively examine the heart or to find flaws in manufactured materials such as welds.
What we do
Ultrasonic Phased Arrays use a multiple element probe, whereby the output pulse from each element is time delayed in such a way, as to produce constructive interference at a specific angle and a specific depth. These time delays can be incremented over a range of pre-defined angles to sweep the beam inside the area of inspection. Due to the possibility to control parameters, such as beam angle and focal distance; this method is very efficient regarding the defect detection and speed of testing. Apart from detecting discontinuities in welds and components, Phased Arrays can also be used for, Thickness Measurements and Corrosion Inspection
Our Technicians design and developed their own scanners to ensure that the inspections cover all the requirement and for accurate repeatability of defect monitoring.
Our service system
Sonatest VEO/VEO + & Prisma
Superior Digital Technology
The VEO+ offers superior data throughput and unsurpassed computational capacity. It delivers fast and accurate results using an impressive 32 channel PA beamformer that provides exceptional SNR, using enhanced digital signal processing.
Data file size is not a concern for the VEO+, with thanks to its 64-bit Linux Operating System, as it can count on a fast 128GB SSD memory capacity allowing you to record vast amounts of information in a single acquisition file.
Remote Control Solution
Using the Sonatest Xpair software application, VEO+ can be fully used and controlled remotely, via a simple network connection. VEO+ now offers Wi-Fi along with its fast GB Ethernet port.
Xpair opens the doors of true mobility in the NDT market. It is a PC-based software application solution to manage data transfer and remote control of instruments in the field wherever a network connection is available. Moreover, with the Xpair Cloud option, a user can access and remotely pilot the instrument of a colleague located 1000s of km away using a mobile or wired internet connection.
Advanced Analysis Software
UTstudio+
UTstudio+ allow inspection data management to be easily done.
Loaded with a comprehensive user interface, data analysis and setup file construction, becomes natural and straight forward. From customized views to additional gates, measurement tools or refined color palettes, UTstudio+ helps one generate extended reports and much more.
Suitable for FMC-TFM, Phased Array and Conventional Ultrasonic Technologies, UTstudio+ is able to accomplish amazing things and get the job done for a multitude of simple advanced applications.
UTview
Loaded with a comprehensive user interface, inspection data and results are now freely accessible to anyone who wants to review them. From customized views to additional gates, measurement tools or refined colour palettes, UTview helps to share results with collaborators to get the job done faster.
Our commitment
Is always to provide a precise and thorough inspection according to the Client’s requirements.
Most popular Questions
What is PAUT testing?
Phased Array Ultrasonics (PA) is an advanced method of Ultrasonic Testing that has applications in Medical Imaging and Industrial Non-Destructive Testing. Common applications are to non-invasively examine the heart or to find flaws in manufactured materials such as welds.
Benefits of working with us
Based on experience, we will always attempt to find an acceptable solution for any unconventional circumstances and needs.
Computerized Radiographic Testing
(CR) uses very similar equipment to Conventional Radiography, except that instead of a film to create the image, an imaging plate (IP) made of a photostimulable phosphor is used.
What we do
Computerized Radiography (CR) is the digital replacement of conventional X-Ray Film Radiography, and offers enormous advantages for inspection tasks – the use of consumables are virtually eliminated and the time to produce an image is drastically shortened.
Our service system
HPX – 1 Plus
- Has the capability to handle Extra Length Plates, custom cut Plates & Rigid Cassettes
- Improved Optics for better Imaging
- 30% Faster throughput on Long Saturated Plates
- Improved Imaging Plate Transport System
- Higher Mechanical Reliability, and a more user-friendly DICONDE compliant software for the best experience in Digital Imaging
Our commitment
Is always to provide a precise and thorough inspection according to the Client’s requirements and needs.
Most Popular Questions
Why is radiography test required?
Radiographic and Ultrasonic Weld Inspections are the two most common methods of Non-Destructive Testing (NDT) used to detect discontinuities within the internal structure of welds. Energy not absorbed by the object, will cause exposure of the Radiographic Film. These areas will appear dark when the film is developed.
How do X rays differ from gamma rays?
X-Rays and Gamma Rays differ only in their source of origin. X-Rays are produced by an X-Ray Generator and Gamma Radiation is the product of Radioactive Atoms. They are both part of the Electromagnetic Spectrum. They are waveforms, as are light rays, microwaves, and radio waves.
How is radiography done?
Industrial Radiography is a method of Non-Destructive Testing where many types of manufactured components can be examined to verify the internal structure and integrity of the specimen. Industrial Radiography can be performed utilizing either X-Rays or Gamma Rays.
Benefits of working with us
Based on experience, we will always attempt to find an acceptable solution for any unconventional circumstance or requirements for our Clientele.
Visual Testing
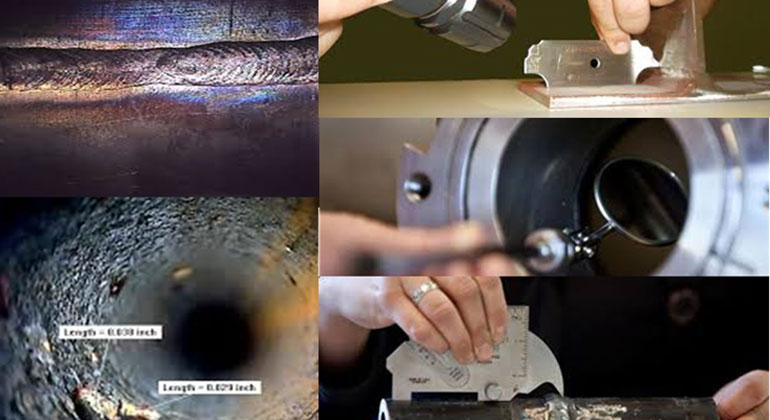
It is relatively easy and low demand. The equipment is used for inspection of only direct and close inaccessible areas, such as tanks, tubes and vessels. The benefits are transparency and understandable reported information. We can measure dimensions. Data storage is simple via images. VT can be applied everywhere, including an object with elevated temperature. Potential users are Weld Workshops, and Assembly Workplaces.
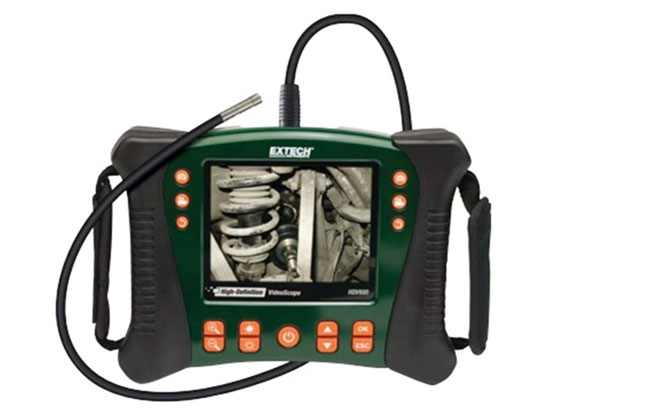
What we do
Our Technicians have the Knowledge of Product and Process, anticipated service conditions, acceptance criteria, and record-keeping
The applications of visual testing include:
- Checking the surface condition of the component
- Checking the alignment of mating surfaces
- Checking the shape of the component
- Checking for evidence of any leakages
- Checking for internal side defects
Our service system
Mechanical or optical aids to perform visual testing
These include such items as:
- Video scope
- Magnifying glasses
- Mirrors
- UV Lights
- Welding Gauges
Our commitment
Is always to provide a precise and thorough inspection according to the Client’s requirements and needs.
Most popular Questions
What is a VT test?
Visual testing is one of the methods of Non-Destructive Testing of Optical Type. It is based on obtaining information about the tested material with the help of visual observation, or of Optical and Measuring Instruments.
Benefits of working with us
Based on experience, we will always attempt to find an acceptable solution for any unconventional circumstance or requirements for our Clientele.
Liquid Penetrant Testing
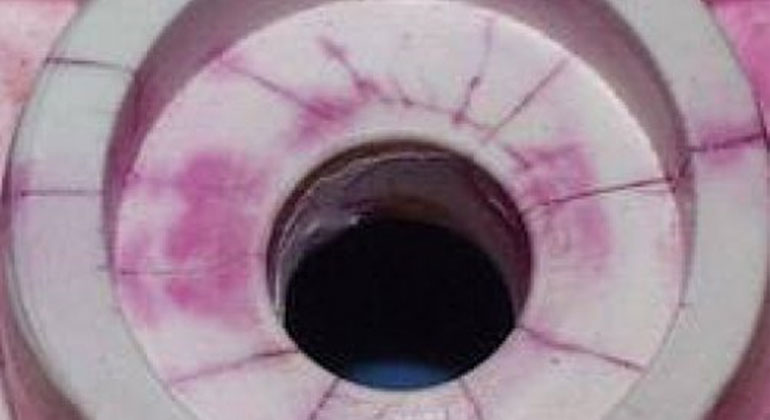
This method is used to find surface defects, not limited to ferrous materials. Do not require any power source, is highly portable and an efficient method. It is generally used where MPT cannot be applied – i.e. where the material is non-ferrous.
What we do
Our Qualified Technicians are specialized in Liquid Penetrant Testing on:
- New Fabricated Welding, Casting & Forgings for any external/surface indications according to applicable specifications and standards
- In-service testing for Fatigue Cracks & Surface Breaking Flaws on Welds, Pins, Bolts and Shafts
Our service system
Penetrant Classification System:
- Type 1: Fluorescent Dye
- Type 2: Visible (Red) Dye
- Method A: Water Washable
- Method B: Post Emulsifiable, lipophilic (oil base)
- Method C: Solvent
Our commitment
Is always to provide a precise and thorough inspection according to the Client’s requirements and needs.
Most Popular Questions
What is the principle of liquid penetrant testing?
The principle of Liquid Penetrant Testing is that the liquid penetrant is drawn into the surface-breaking crack, by capillary action and excess surface penetrant is then removed; a developer (typically a dry powder) is then applied to the surface, to draw out the penetrant in the crack, which produce a surface indication.
Which type of penetrant is most sensitive?
Fluorescent Penetrant systems are more sensitive than visible penetrant systems, because the eye is drawn to the glow of the Fluorescing Indication.
Which type of developer is considered the most sensitive?
Non-aqueous developers are generally recognized as the most sensitive when properly applied. There is less agreement on the performance of dry and aqueous wet developers, although the aqueous developers are usually considered more sensitive.
Benefits of working with us
Based on experience, we will always attempt to find an acceptable solution for any unconventional circumstance or requirements for our Clientele.
Magnetic Particle Testing
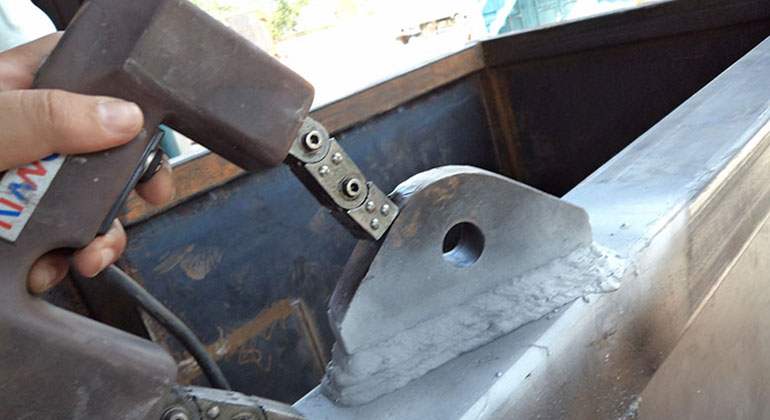
What we do
Our Qualified Technicians are specialized in Magnetic Particle Testing on:
- New Fabricated Welding, Casting & Forgings for any external/surface indications according to applicable specifications and standards
- In-service testing for Fatigue Cracks, Surface Breaking Flaws on Welds, Pins, Bolts and Shafts
Our service system
All our Magnetic Particle Testing Equipment are Calibrated and tested before each shift.
Permanent Magnets: Used for remote areas and isolated inspections
AC Yokes: To use for wet and dry visible and ultraviolet
AC Yokes with Battery packs: For areas where AC yokes are required, where there is no access to electrical power
Our commitment
Is always to provide a precise and thorough inspection according to the Client’s requirements and needs.
Most Popular Questions
What is MPT test?
Magnetic Particle Testing (MPT), also referred to as Magnetic Particle Inspection, is a non-destructive examination (NDE) Technique used to detect surface and slightly sub-surface flaws in most ferromagnetic materials such as iron, nickel, cobalt, and some of their alloys
Can you magnetic particle inspect stainless steel?
It is true that you can perform Magnetic Particle Testing on Ferritic Stainless Steel. The easiest method of determining if the material can be Magnetic Particle Inspected is to see if a Permanent Magnet is attracted to the material. The three elements which are Ferromagnetic: Iron, Nickel and Cobalt.
What is the basic principle of magnetic particle testing?
In theory, Magnetic Particle Inspection (MPI) is a relatively simple concept. It can be considered as a combination of two Non-Destructive Testing methods: Magnetic Flux Leakage Testing and Visual Testing. Consider the case of a bar magnet, it has a magnetic field in, and around the magnet.
Benefits of working with us
Based on experience, we will always attempt to find an acceptable solution for any unconventional circumstance or requirements for our Clientele.